Dunkley International
Industrial Fruit Processing Equipment, Parts, And Service
The International Standard in Cherry Processing Equipment
Based in Kalamazoo, Michigan USA we provide service throughout the world where cherries are grown. Our principal business consists of the design & manufacturing of built-to-last proven cherry pitters along with service and parts supply. Dunkley designs innovative products and services which are tailored to customer needs for efficiency and throughput. Dunkley is a recognized leader within the tart and sweet cherry industry for its depth of experience in supporting cherry production for over 100 years.
Pitting cherries is both an art and a science. Our expert staff understands cherry processing and the importance of pit removal for providing an enjoyable consumer eating experience.
Our mission is simple: Be the best little cherry pitting company in the business!
A Proud Subsidiary of Cherry Central, LLC
Cherry Central’s purpose is to create a legacy of family farms gathering to market and sell sustainable fruit products, improve the lives of customers and maximize success for growers. Cherry Central is focused on expanding products in all market channels and walks of life for generations to come. Founded in 1973, Cherry Central operates as a cooperative for its grower members throughout North America and is based in Traverse City, Michigan. Cherry Central is vertically integrated from the field to finished product. Dunkley International is a key strategic fit for this organization of grower owners who are leaders in the cherry industry.
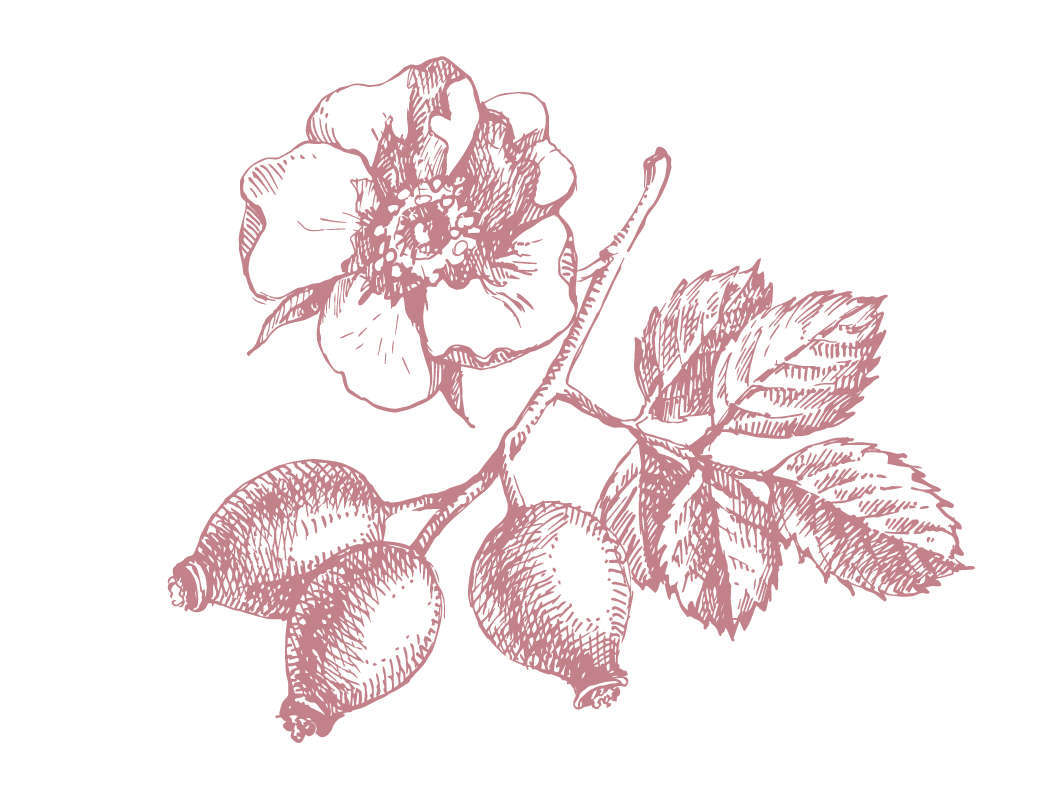
Contact Dunkley International
Fruit Processing Machinery, Parts, and Service
Custom Fruit Processing Equipment
Our products range from a small table top pitter which is designed for small boutique/farm market settings to a commercial pitter for use at large consumer products companies who market products into the dessert markets in food service and grocery stores.
Replacement Parts
Preventative maintenance is critical to supporting the longevity of equipment like Dunkley pitters. Annual audit of the equipment and planning for replacement parts helps extend the life of Dunkley pitters. Dunkley keeps significant stock on hand of replacement parts to prevent back orders and out-of-stock situations. Well maintained Dunkley pitters are built to last.
Service and Repair
With over 101 years of combined experience, our team is ready to meet your service and repair needs. We’ll convert “work horse” cast iron pitters with current stainless steel technology and we base our core business on preventative maintenance. We plan, do, check and act in accordance with continuous improvement practices. No request is too simple or complex. You need needles sharpened? Call on us.
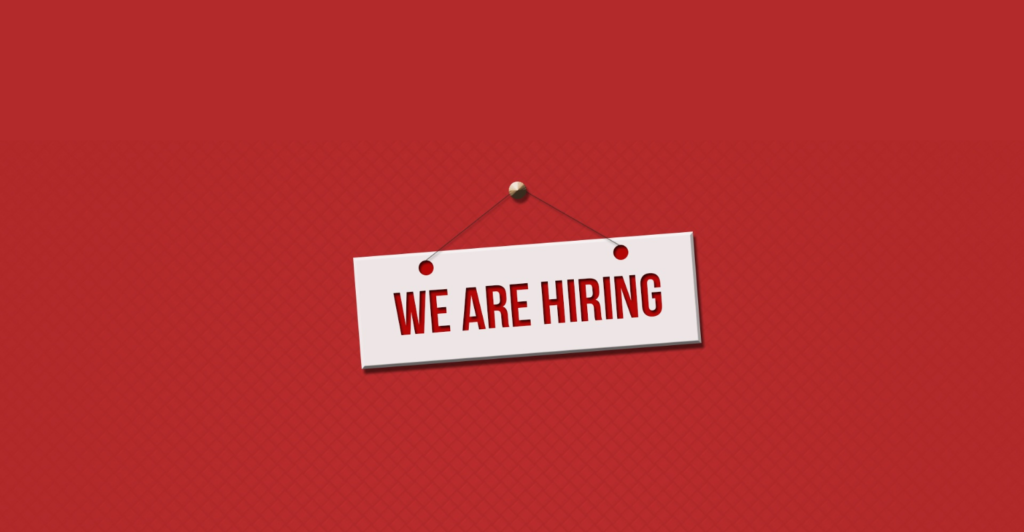
Dunkley News
Dunkley International is now accepting new work for the 2024 calendar year! To find out more about our open positions, please contact hr@cherrycentral.com.
See Our Fruit Processors In Action
The simple design and well-built construction of our processing equipment makes for versatile adjustments and easy maintenance. You can rely on our equipment for years to come. We are excited to offer our current line-up: the SSP-2800 Cherry Pitter, SSP-1500 Jr. Pitter, TTP-200 Table Top, NS-100 Needle Sharpener, SSP-5000 Cranberry Piercer, SSP-3000 Large Cherry Pitter, Cherry Destemmer, and Blueberry Destemmer. We offer service and support for Dunkley’s Legacy Products as well, including the widely used SSP-2000 Pitter, original Cast-Iron Pitter, Dunkley International Jr. Pitter, and Sizing/Eliminator Chains.
For More Information Please Contact:
Jack Minear
Facility Manager/Senior Planner Dunkley International, Inc.
Phone 269.343.5583
Jminear@dunkleyintl.com
Vince Higgs
National Sales Manager – Retail
Cell 231.944.0067
Vhiggs@cherrycentral.com
Lizabeth Danek
Sales and Marketing Development
Cell 509.290.7332
Ldanek@cherrycentral.com